Centralized vs Decentralized Inventory Management
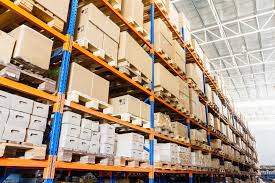
There is a key issue relative to Inventory Replenishment Management at companies with multiple warehouses or stocking branches. Do you let each of the locations manage their own inventories, or do you create inventory replenishment purchase orders centrally for each location with only a minimum of input from the separate locations? A summary of the advantages and disadvantages to the two options are generally as follows:
Advantages of Decentralized Inventory Management
The key advantage to having inventory decisions take place locally is that personnel are aware of local factors and upcoming events. They are in a position to anticipate special circumstances like promotions or or events that may be strictly local in nature. Additionally, they may be aware of unique input regarding the plans of major customers. Allowing the local office to control and manage their inventory levels fosters a sense of ownership and control that can be desirable.
Disadvantages of Decentralized Inventory Management
The biggest disadvantage to local control is that local personnel may lack well developed inventory management skills and operate on a highly subjective basis, even when fairly sophisticated tools are available. Local personnel without a global view may try to manage inventory by “feel” rather than by formula.
There can also be a tendency to overreact to events which are otherwise transient in nature. Local management can also have a strong bias for high inventories being visually present. They may fail to take advantage of the inventory that is in the pipeline or which exists in another warehouse that may be able to provide inventory coverage without a vendor reorder. This can lead to higher than optimal levels of inventory on the warehouse floor.
Advantages of Centralized Inventory Management
Stronger, more professional inventory managers may be employed who are further removed from day-to-day events that cause reactionary actions. These individuals can be thoroughly trained in both the general principles of inventory management and the particular philosophy and system being used to drive the ordering process at your company. Special buying opportunities can be more effectively explored since the information for all locations resides in the central system and the individual can more easily adopt a total company “big picture” view.
Disadvantages of Centralized Inventory Management
Centralization can lead to problems associated with lack of knowledge or understanding of local conditions at each loacation. A one-size-fits-all attitude can easily develop which can lead to lost opportunities and unintentional overstocks. The centralized approach can also lead to local management feeling disenfranchised by not having control of their inventories. The lack of ownership can stifle innovation and impact productivity in local offices.
General Discussion
In the marketplace, the pendulum swings between these two approaches. Many have a fundamental bias for decentralization in business functions. There is something appealing in the idea of people closest to the problems and action making the key decisions that impact their operations. Others lean toward the centralized approach because of the high level of control available to the central planners especially in the area of finance and inventory investment capital.
If local management had the technical strength and personal discipline to manage their inventories using a strong software system, and not arbitrarily override the recommendations, then the market would unquestionably favor local control. Unfortunately, this ideal set of circumstances very rarely exists. The typical situation is that the problems mentioned above of overreaction and bias to having inventory physically in view, overwhelm all other considerations.
There has been a lot of annecdotal evidence observed time and time again siting cases of local management overriding perfectly fine order levels on the basis of some general “gut feeling” that was frankly without merit. As an example, one company created replenishment orders centrally and then sent it down to the branches for their input. Ideally, the only overrides made by local management should have been based on unique local circumstances (e.g., we are running a special flyer in the local newspaper next month and we better inflate our reorder of those items). Instead, the replenishment orders routinely came back with each item crossed out and replaced by something higher. When asked for the rational for the changes, the comment was, “Oh, they just seemed a bit low.” Unfortunately this is typical, and sometimes represents the inability of local management to realize that they had more effective inventory than met the eye. It was actually in the pipeline and/or in the central warehouse as a backup.
Centralizing inventory management only works if the software tools driving the replenishment orders are sufficiently robust. With a weak system driving the inventory status, there will be innumerable questionable situations that arise, and very possibly a drop in fill rates. Local management will then react very negatively and a total collapse of the system can take place.
The NBDS solution quite frankly, has the power and feature set to insure that both centralized and decentralized inventory replenishment management can achieve optimal inventory levels. Our MARS Inventory Replenishment workstation runs off of a centralized data store that insures optimal inventory level calculation across all locations. The calculations can include localized seasonality indexes as well as auto-generated indexes based on the individual performance of each item in each local market. Purchasing can be done either centrally or in the local office while sharing the same global knowledge base.
Additionally, our Venus Sales Forecast solution allows input of special buy considerations and other economic trade-offs at every level (local and company wide) simultaneously. Using these facilities (along with a well defined process) allows the “best of both worlds” scenario where corporate financial objectives and local market conditions play together for a better overall outcome.
Recommendation
Our final recommendation is to manage inventories through a centrally managed solution such as MARS and VENUS from [NBDS] (http://www.nbds.com). This allows buyers to use MARS while either co-located or distributed while taking advantage of a mechanism like VENUS by which local management can offer input regarding local events. At the same time sales and brand management executives can use VENUS to supply overrides based on overal company needs and opportunities. This mechanism should however, be paired with a strongly defined process to insure that any overrides are based on bona fide situations that are based purely on business insight rather than “gut feel” reactions.
To learn more about how Mars can help, see our offer below.